精益管理中的一個流生產(chǎn)模式
日期:2017-03-07 / 人氣: / 來源:m.wtport.com / 熱門標(biāo)簽: 精益管理
一個流生產(chǎn)模式是精益管理準(zhǔn)時化生產(chǎn)的物流形式,是實現(xiàn)準(zhǔn)時化生產(chǎn)的基礎(chǔ)。
1.概念
一個流生產(chǎn)是指從毛坯投入到成品產(chǎn)出的整個制造加工過程,零件始終處于不停滯、不堆積、不超越,按節(jié)拍一個一個的流動的生產(chǎn)方法。它的含義包括:
1)每道工序加工完一個制件后立即流到下一工序;
2)工序間的在制品數(shù)量不超過緊前工序的裝夾數(shù)量;
3)制件的運(yùn)動不間斷、不超越、不落地;
4)生產(chǎn)工序、檢驗工序和運(yùn)輸工序合為一體;
5)只有合格的產(chǎn)品才允許往下道工序流
2.實施一個流生產(chǎn)的優(yōu)點(diǎn)
1)生產(chǎn)周期短;
2)在制品少;
3)場地占用少;
4)適應(yīng)市場與計劃的變更;
5)避免批量質(zhì)量缺陷;
6)易暴露問題點(diǎn);
3.實現(xiàn)一個流生產(chǎn)應(yīng)遵循的原則
1) 信息流與物流同步原則
一個流生產(chǎn)要求在沒有庫存的前提下,實現(xiàn)在必要的時刻得到必要的零件,為此,應(yīng)使各種零部件的生產(chǎn)和供應(yīng)完全同步,整個生產(chǎn)按比例、協(xié)調(diào)地連續(xù)生產(chǎn),按照后工序的需要安排投入和產(chǎn)出。物流同步要求避免以下情況:
a. 超過裝夾數(shù)量的零件到達(dá)某工序,零件出現(xiàn)等候和積壓;
b. 某工序所需要的零件不同時到達(dá),出現(xiàn)滯后或超前;
c. 前后工序生產(chǎn)不均衡;
d. 因某一工序的問題使物流出現(xiàn)停頓;
為實現(xiàn)物流的同步,要求班組不斷開展“5S”活動。
2)內(nèi)部服務(wù)原則
實現(xiàn)一個流生產(chǎn)要求每一道加工工序無缺陷、無故障,若制件出現(xiàn)缺陷,要停掉生產(chǎn)線,要強(qiáng)行把有缺陷的制件流下去,無論何種選擇都將引起成本的上升。因此,一個流要求每一道工序嚴(yán)格控制工作質(zhì)量,做到質(zhì)量在過程中控制,遵循內(nèi)部用戶原則。其含義是:
每一道工序是前道工序的用戶
每一道工序是后道工序的供貨商
每一道工序只接受前道工序合格的產(chǎn)品
每一道工序只生產(chǎn)合格的產(chǎn)品
每一道工序只提供合格的產(chǎn)品給后道工序
遵循服務(wù)用戶原則的具體方法是開展自檢、互檢,并嚴(yán)格按工藝操作規(guī)范進(jìn)行生產(chǎn)。
3)消除浪費(fèi)原則
一個流生產(chǎn)的目的是減少在制品,使生產(chǎn)中存在的浪費(fèi)現(xiàn)象暴露出來,并不斷排除,使
成本下降。這些浪費(fèi)現(xiàn)象包括:
在制品過剩
供貨拖拉
排除設(shè)備故障的時間長
信息交流不暢通
工藝紀(jì)律差
上述的任何一個問題都會阻礙一個流生產(chǎn)方式的順利進(jìn)行,因此,必須采取積極的態(tài)度
解決這些問題,為實現(xiàn)一個流生產(chǎn)方式創(chuàng)造條件。
4.一個流推行實施步驟(根據(jù)本人實際推行一款產(chǎn)品為案例)
1)案例背景:根據(jù)財務(wù)報表顯示“迪卡儂4.2”處于盈虧平衡點(diǎn),由于公司訂單量急劇下滑,生產(chǎn)各單位必須從內(nèi)部尋找改善,提高實現(xiàn)改款產(chǎn)品盈利
2)單件流生產(chǎn)模式啟動會議:成立改善小組并任命各小組成員工作職責(zé),培訓(xùn)小組成員單件流生產(chǎn)模式相關(guān)知識體系,指導(dǎo)班組長完成以下任務(wù)3)4)5)6)7)
3)收集生產(chǎn)線改善前數(shù)據(jù):各工種人員數(shù)量、作業(yè)員掌握技能、生產(chǎn)人員出勤時間、各工序標(biāo)準(zhǔn)工時、各工序分配狀況、人員及設(shè)備現(xiàn)場布局、生產(chǎn)在制品數(shù)量及批次、成品檢驗合格率、日均產(chǎn)出數(shù)量
4)生產(chǎn)現(xiàn)狀數(shù)據(jù)分析:生產(chǎn)及工藝流程圖、人員的配置及生產(chǎn)線平衡率、生產(chǎn)線-la. yout、生產(chǎn)力評核-PPH、價值流程圖
5)重新規(guī)劃生產(chǎn)線體:
a. 根據(jù)客戶Fc. ST,確定生產(chǎn)節(jié)拍
b. 規(guī)劃生產(chǎn)流程:根據(jù)工藝流程圖、生產(chǎn)節(jié)拍、各制程的加工時間、人力時間,計算出各個制程的設(shè)備需求數(shù)和作業(yè)人員的需求數(shù)及技能要求,規(guī)劃出生產(chǎn)流程圖
c. 布置生產(chǎn)線體:根據(jù)生產(chǎn)流程圖順序、人員搬運(yùn)路線盡量減少、作業(yè)臺方便操作為原則進(jìn)行現(xiàn)場生產(chǎn)布局(關(guān)鍵工位使用生產(chǎn)看板,用于指導(dǎo)物料及時搬運(yùn)及投送)
6)現(xiàn)場實施單件流生產(chǎn)
a. 召開生產(chǎn)會議,班組長負(fù)責(zé)安排并指導(dǎo)各工位人員工作內(nèi)容及注意事項,
b. 搜集改善后現(xiàn)場數(shù)據(jù):日均產(chǎn)出數(shù)量及成品檢驗合格率
c. 異常工時的統(tǒng)計及分析
7)項目成果分享以及持續(xù)改善點(diǎn)歸納總結(jié)
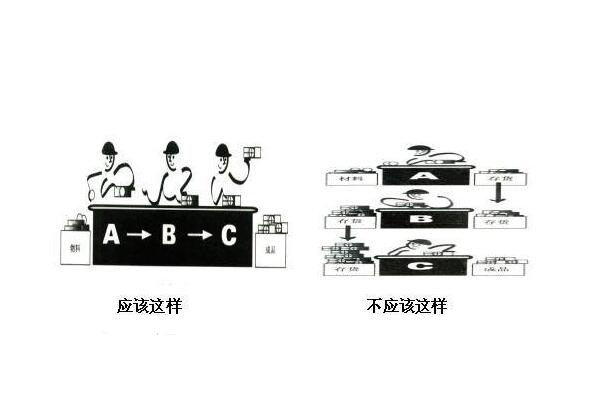
一個流生產(chǎn)是指從毛坯投入到成品產(chǎn)出的整個制造加工過程,零件始終處于不停滯、不堆積、不超越,按節(jié)拍一個一個的流動的生產(chǎn)方法。它的含義包括:
1)每道工序加工完一個制件后立即流到下一工序;
2)工序間的在制品數(shù)量不超過緊前工序的裝夾數(shù)量;
3)制件的運(yùn)動不間斷、不超越、不落地;
4)生產(chǎn)工序、檢驗工序和運(yùn)輸工序合為一體;
5)只有合格的產(chǎn)品才允許往下道工序流
2.實施一個流生產(chǎn)的優(yōu)點(diǎn)
1)生產(chǎn)周期短;
2)在制品少;
3)場地占用少;
4)適應(yīng)市場與計劃的變更;
5)避免批量質(zhì)量缺陷;
6)易暴露問題點(diǎn);
3.實現(xiàn)一個流生產(chǎn)應(yīng)遵循的原則
1) 信息流與物流同步原則
一個流生產(chǎn)要求在沒有庫存的前提下,實現(xiàn)在必要的時刻得到必要的零件,為此,應(yīng)使各種零部件的生產(chǎn)和供應(yīng)完全同步,整個生產(chǎn)按比例、協(xié)調(diào)地連續(xù)生產(chǎn),按照后工序的需要安排投入和產(chǎn)出。物流同步要求避免以下情況:
a. 超過裝夾數(shù)量的零件到達(dá)某工序,零件出現(xiàn)等候和積壓;
b. 某工序所需要的零件不同時到達(dá),出現(xiàn)滯后或超前;
c. 前后工序生產(chǎn)不均衡;
d. 因某一工序的問題使物流出現(xiàn)停頓;
為實現(xiàn)物流的同步,要求班組不斷開展“5S”活動。
2)內(nèi)部服務(wù)原則
實現(xiàn)一個流生產(chǎn)要求每一道加工工序無缺陷、無故障,若制件出現(xiàn)缺陷,要停掉生產(chǎn)線,要強(qiáng)行把有缺陷的制件流下去,無論何種選擇都將引起成本的上升。因此,一個流要求每一道工序嚴(yán)格控制工作質(zhì)量,做到質(zhì)量在過程中控制,遵循內(nèi)部用戶原則。其含義是:
每一道工序是前道工序的用戶
每一道工序是后道工序的供貨商
每一道工序只接受前道工序合格的產(chǎn)品
每一道工序只生產(chǎn)合格的產(chǎn)品
每一道工序只提供合格的產(chǎn)品給后道工序
遵循服務(wù)用戶原則的具體方法是開展自檢、互檢,并嚴(yán)格按工藝操作規(guī)范進(jìn)行生產(chǎn)。
3)消除浪費(fèi)原則
一個流生產(chǎn)的目的是減少在制品,使生產(chǎn)中存在的浪費(fèi)現(xiàn)象暴露出來,并不斷排除,使
成本下降。這些浪費(fèi)現(xiàn)象包括:
在制品過剩
供貨拖拉
排除設(shè)備故障的時間長
信息交流不暢通
工藝紀(jì)律差
上述的任何一個問題都會阻礙一個流生產(chǎn)方式的順利進(jìn)行,因此,必須采取積極的態(tài)度
解決這些問題,為實現(xiàn)一個流生產(chǎn)方式創(chuàng)造條件。
4.一個流推行實施步驟(根據(jù)本人實際推行一款產(chǎn)品為案例)
1)案例背景:根據(jù)財務(wù)報表顯示“迪卡儂4.2”處于盈虧平衡點(diǎn),由于公司訂單量急劇下滑,生產(chǎn)各單位必須從內(nèi)部尋找改善,提高實現(xiàn)改款產(chǎn)品盈利
2)單件流生產(chǎn)模式啟動會議:成立改善小組并任命各小組成員工作職責(zé),培訓(xùn)小組成員單件流生產(chǎn)模式相關(guān)知識體系,指導(dǎo)班組長完成以下任務(wù)3)4)5)6)7)
3)收集生產(chǎn)線改善前數(shù)據(jù):各工種人員數(shù)量、作業(yè)員掌握技能、生產(chǎn)人員出勤時間、各工序標(biāo)準(zhǔn)工時、各工序分配狀況、人員及設(shè)備現(xiàn)場布局、生產(chǎn)在制品數(shù)量及批次、成品檢驗合格率、日均產(chǎn)出數(shù)量
4)生產(chǎn)現(xiàn)狀數(shù)據(jù)分析:生產(chǎn)及工藝流程圖、人員的配置及生產(chǎn)線平衡率、生產(chǎn)線-la. yout、生產(chǎn)力評核-PPH、價值流程圖
5)重新規(guī)劃生產(chǎn)線體:
a. 根據(jù)客戶Fc. ST,確定生產(chǎn)節(jié)拍
b. 規(guī)劃生產(chǎn)流程:根據(jù)工藝流程圖、生產(chǎn)節(jié)拍、各制程的加工時間、人力時間,計算出各個制程的設(shè)備需求數(shù)和作業(yè)人員的需求數(shù)及技能要求,規(guī)劃出生產(chǎn)流程圖
c. 布置生產(chǎn)線體:根據(jù)生產(chǎn)流程圖順序、人員搬運(yùn)路線盡量減少、作業(yè)臺方便操作為原則進(jìn)行現(xiàn)場生產(chǎn)布局(關(guān)鍵工位使用生產(chǎn)看板,用于指導(dǎo)物料及時搬運(yùn)及投送)
6)現(xiàn)場實施單件流生產(chǎn)
a. 召開生產(chǎn)會議,班組長負(fù)責(zé)安排并指導(dǎo)各工位人員工作內(nèi)容及注意事項,
b. 搜集改善后現(xiàn)場數(shù)據(jù):日均產(chǎn)出數(shù)量及成品檢驗合格率
c. 異常工時的統(tǒng)計及分析
7)項目成果分享以及持續(xù)改善點(diǎn)歸納總結(jié)
作者:博革咨詢