博革精益轉(zhuǎn)型之現(xiàn)場標(biāo)準(zhǔn)化
日期:2016-11-25 / 人氣: / 來源:m.wtport.com / 熱門標(biāo)簽: 博革精益轉(zhuǎn)型
現(xiàn)場標(biāo)準(zhǔn)化是博革咨詢公司獨(dú)有的BPS系統(tǒng)中的要素之一,可以快速在企業(yè)一部分區(qū)域快速形成標(biāo)準(zhǔn)化、可視化、績效穩(wěn)定的生產(chǎn)現(xiàn)場,作為企業(yè)標(biāo)桿進(jìn)而推廣至整個生產(chǎn)部門?,F(xiàn)場標(biāo)準(zhǔn)化,經(jīng)博革咨詢公司多年打磨,在為企業(yè)樹立現(xiàn)場標(biāo)桿方面堪稱完美,是企業(yè)實(shí)現(xiàn)生產(chǎn)效率提升的利器。
BPS系統(tǒng)是博革集團(tuán)以二十多年現(xiàn)場咨詢經(jīng)驗(yàn),集中日韓三個國家的咨詢團(tuán)隊(duì),結(jié)合TPS/GMS/FPS以及WCM等一流經(jīng)營理念,共同開發(fā)的企業(yè)精益轉(zhuǎn)型升級系統(tǒng)。
現(xiàn)場標(biāo)準(zhǔn)化是位于BPS系統(tǒng)中——運(yùn)營系統(tǒng)——生產(chǎn)管理下的一個要素,包含以下三個內(nèi)容:精益布局、可視化、標(biāo)準(zhǔn)化。博革咨詢的現(xiàn)場標(biāo)準(zhǔn)化因其細(xì)致有效而著稱,要實(shí)現(xiàn)現(xiàn)場標(biāo)準(zhǔn)化,通常需要一個月的時間,這就是博革咨詢常說的“一月一標(biāo)桿”。
現(xiàn)場標(biāo)準(zhǔn)化的第一項(xiàng)就是精益布局,精益布局是現(xiàn)場標(biāo)準(zhǔn)化的重中之重,要讓現(xiàn)場形成按節(jié)拍流動的布局,如何找到這個節(jié)拍呢?
首先我們需要繪制價(jià)值流圖來作分析,這樣可以對生產(chǎn)現(xiàn)場的所有問題做到大致了解。接下來我們就可以根據(jù)企業(yè)對生產(chǎn)速度的要求來設(shè)定“節(jié)拍”了,即多久生產(chǎn)一臺?知道我們要做達(dá)成什么目標(biāo),那么就可以開始設(shè)計(jì)布局了。
設(shè)計(jì)布局是考驗(yàn)真功夫的時候,大致需要從大到小在以下三個方面設(shè)計(jì)布局:線體布局設(shè)計(jì)、工位布局設(shè)計(jì)、線邊物料設(shè)計(jì)。
線體布局設(shè)計(jì),就是合理設(shè)計(jì)生產(chǎn)線,至于采用一字線、U型線、還是復(fù)合線,都要咨詢顧問詳細(xì)計(jì)算規(guī)劃,需要注意的方面也很多,這里就不展開談了。
工位布局設(shè)計(jì),需要考慮以下方面:面積適當(dāng)、零件的排列便于使用、工具放置標(biāo)準(zhǔn)化、物料續(xù)供、信息管理、目視控制、質(zhì)量監(jiān)控、工人走動及作業(yè)標(biāo)準(zhǔn)等。
線邊物料設(shè)計(jì),可以遵循作業(yè)布置五項(xiàng)原則,即:不挑選、不尋找、不轉(zhuǎn)身、不離開、不彎腰。應(yīng)當(dāng)減少工人周期時間的波動、減少工位上的零件、確保標(biāo)準(zhǔn)化作業(yè)、易補(bǔ)充物料、建立良好的人機(jī)工程。
接下來要做流動瓶頸改善,流動瓶頸改善有——快速切換SMED、低成本自動化設(shè)計(jì)、IE改善、PFMEA。
快速切換SMED,企業(yè)通常不會只生產(chǎn)一種型號的產(chǎn)品,因此確??焖偾袚Q生產(chǎn)線,也是提高生產(chǎn)率的重要指標(biāo)。
低成本自動化,分為裝配LCIA和搬運(yùn)LCIA兩大項(xiàng),其中裝配LCIA比較專業(yè),這里我們說一下搬運(yùn)LCIA的基本思路。基本原則是要減少搬運(yùn)的距離、減少存取的動作、減少搬運(yùn)的距離。原材料的搬運(yùn)應(yīng)當(dāng)確保百分之百為良品、容器容量標(biāo)準(zhǔn)、多回少量巡回混載。制品的搬運(yùn)應(yīng)當(dāng)實(shí)現(xiàn)1/0一致;本工程完成的“放置點(diǎn)”,即為下個工程的“拿取點(diǎn)”;一次搬運(yùn)一個;利用低成本重力滑道;一面搬運(yùn)一面工作等。成品的搬運(yùn)應(yīng)當(dāng)做到完成的直接放入貨柜車內(nèi);采取后拉式接單生產(chǎn);生產(chǎn)交期要短于交貨交期等。
IE改善,IE工業(yè)工程學(xué)是現(xiàn)場改善的基礎(chǔ),博革咨詢將針對現(xiàn)場班組長和工程師團(tuán)隊(duì),細(xì)致講授IE實(shí)戰(zhàn)手法,帶領(lǐng)他們逐步進(jìn)行IE改善活動,確保全員參與改善活動,實(shí)現(xiàn)生產(chǎn)效率的全面提升。IE改善包含兩大內(nèi)容:制造方式的浪費(fèi)改善和管理方式的浪費(fèi)改善。其中制造方式包括工序分析、搬運(yùn)分析、運(yùn)轉(zhuǎn)分析;管理方式包括:LOB分析、作業(yè)分析、效率分析等。
PFMEA是制程失效模式及效果分析的英文簡稱。由產(chǎn)品工程師、制造工程師、質(zhì)量工程師、物流工程師、生管人員等組成的橫向?qū)<倚〗M,逐個對工位(工序)進(jìn)行現(xiàn)場審計(jì)、診斷出工位(工序)的“過程要素”是否達(dá)到“工序的目的”。
以上就是現(xiàn)場標(biāo)準(zhǔn)化的精益布局的主要內(nèi)容,完成時間約為兩周?,F(xiàn)場標(biāo)準(zhǔn)化的第二項(xiàng)內(nèi)容為“可視化”,即全面可視化現(xiàn)場。
生產(chǎn)現(xiàn)場全面可視化主要包含以下七大內(nèi)容:
第一,安全可視化——對產(chǎn)線安全設(shè)施設(shè)備進(jìn)行目視化管理,讓員工重視:危險(xiǎn)區(qū)域識別、安全天數(shù)展示、安全隱患識別,并用可視化的方式來展示具體操作步驟。
第二,質(zhì)量可視化——明確關(guān)鍵工序的位置及相關(guān)事項(xiàng),關(guān)鍵工序指標(biāo)的趨勢管理;首件產(chǎn)品封樣管理;生產(chǎn)不良品展示,識別不良品,明確不良品的判定標(biāo)準(zhǔn)和責(zé)任人員等。
第三,生產(chǎn)可視化——明確班組劃分、明確生產(chǎn)線工位名稱;明確產(chǎn)品屬性及狀態(tài);將作業(yè)指導(dǎo)書展示在現(xiàn)場;明確物流小車責(zé)任人,周轉(zhuǎn)次數(shù)等相關(guān)信息;生產(chǎn)管理文件可視化;
規(guī)定班組會議區(qū)域;時段目標(biāo)與實(shí)際產(chǎn)出可視化,及時識別異常;物料信息目視化,以免拿錯;工裝器具進(jìn)行形跡管理,易拿易管等。
第四,成本可視化——將成本的相關(guān)信息可視化,明確成本的損失點(diǎn)和控制要素。
第五,設(shè)備可視化——設(shè)備操作規(guī)程、維護(hù)規(guī)程可視化;設(shè)備名稱、設(shè)備主人、維護(hù)周期目視化;標(biāo)示計(jì)量界限范圍;明確設(shè)備的狀態(tài),正常運(yùn)行以及是否處于維修等。
第六,環(huán)境可視化——明確清掃工具放置位置,集中管理;規(guī)定水杯擺放,以免有傷產(chǎn)品;垃圾分來擺放等。
第七,人員可視化——人員培訓(xùn)后方可持證上崗;區(qū)別不同區(qū)域不同級別的人員;多技能工認(rèn)證可視化;描述班組的培訓(xùn)計(jì)劃、合理化建議、優(yōu)秀員工、5S、學(xué)習(xí)園地、員工風(fēng)采等。
以上是現(xiàn)場標(biāo)準(zhǔn)化第二項(xiàng)要素“可視化”的主要內(nèi)容,完成時間約為一周?,F(xiàn)場標(biāo)準(zhǔn)化的第三項(xiàng)內(nèi)容就是“標(biāo)準(zhǔn)化”。這里的標(biāo)準(zhǔn)化指的是管理層面的標(biāo)準(zhǔn)化,即實(shí)現(xiàn)現(xiàn)場績效的穩(wěn)定。
管理標(biāo)準(zhǔn)化遵循以下七大“標(biāo)準(zhǔn)”:
第一,數(shù)據(jù)收集標(biāo)準(zhǔn)——收集每日生產(chǎn)數(shù)據(jù),制定標(biāo)準(zhǔn)。
第二,進(jìn)度管理標(biāo)準(zhǔn)——明確現(xiàn)場管理人員的進(jìn)度標(biāo)準(zhǔn)。
第三,自工序完結(jié)標(biāo)準(zhǔn)——以關(guān)鍵工序?yàn)橹?,進(jìn)行自查互查。
第四,異常響應(yīng)機(jī)制——A3問題改善、安燈應(yīng)用、分層響應(yīng)機(jī)制、問題處理流程、異常響應(yīng)流程。
第五,現(xiàn)場早會標(biāo)準(zhǔn)——制定早會流程、會議手冊等。
第六,交接班管理標(biāo)準(zhǔn)——推廣班組長日志,明確關(guān)鍵指標(biāo)。
第七,班組績效管理——指標(biāo)討論決定、考核規(guī)定展示、績效可視化、績效核定標(biāo)準(zhǔn)可視化、月度績效考核展示、班組綜合指標(biāo)展示。
以上所有就是博革咨詢現(xiàn)場標(biāo)準(zhǔn)化的簡單介紹,如您需要更多資料或案例,請聯(lián)系客服或給我們留言。
BPS系統(tǒng)是博革集團(tuán)以二十多年現(xiàn)場咨詢經(jīng)驗(yàn),集中日韓三個國家的咨詢團(tuán)隊(duì),結(jié)合TPS/GMS/FPS以及WCM等一流經(jīng)營理念,共同開發(fā)的企業(yè)精益轉(zhuǎn)型升級系統(tǒng)。
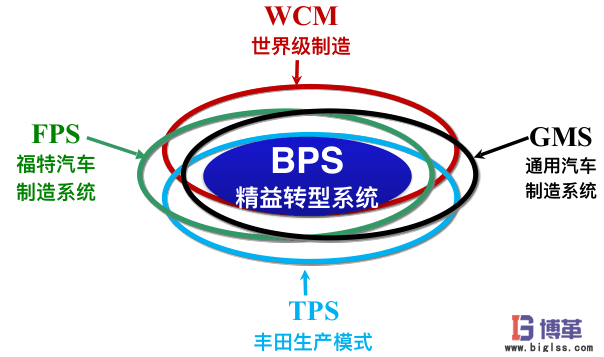
現(xiàn)場標(biāo)準(zhǔn)化的第一項(xiàng)就是精益布局,精益布局是現(xiàn)場標(biāo)準(zhǔn)化的重中之重,要讓現(xiàn)場形成按節(jié)拍流動的布局,如何找到這個節(jié)拍呢?
首先我們需要繪制價(jià)值流圖來作分析,這樣可以對生產(chǎn)現(xiàn)場的所有問題做到大致了解。接下來我們就可以根據(jù)企業(yè)對生產(chǎn)速度的要求來設(shè)定“節(jié)拍”了,即多久生產(chǎn)一臺?知道我們要做達(dá)成什么目標(biāo),那么就可以開始設(shè)計(jì)布局了。
設(shè)計(jì)布局是考驗(yàn)真功夫的時候,大致需要從大到小在以下三個方面設(shè)計(jì)布局:線體布局設(shè)計(jì)、工位布局設(shè)計(jì)、線邊物料設(shè)計(jì)。
線體布局設(shè)計(jì),就是合理設(shè)計(jì)生產(chǎn)線,至于采用一字線、U型線、還是復(fù)合線,都要咨詢顧問詳細(xì)計(jì)算規(guī)劃,需要注意的方面也很多,這里就不展開談了。
工位布局設(shè)計(jì),需要考慮以下方面:面積適當(dāng)、零件的排列便于使用、工具放置標(biāo)準(zhǔn)化、物料續(xù)供、信息管理、目視控制、質(zhì)量監(jiān)控、工人走動及作業(yè)標(biāo)準(zhǔn)等。
線邊物料設(shè)計(jì),可以遵循作業(yè)布置五項(xiàng)原則,即:不挑選、不尋找、不轉(zhuǎn)身、不離開、不彎腰。應(yīng)當(dāng)減少工人周期時間的波動、減少工位上的零件、確保標(biāo)準(zhǔn)化作業(yè)、易補(bǔ)充物料、建立良好的人機(jī)工程。
接下來要做流動瓶頸改善,流動瓶頸改善有——快速切換SMED、低成本自動化設(shè)計(jì)、IE改善、PFMEA。
快速切換SMED,企業(yè)通常不會只生產(chǎn)一種型號的產(chǎn)品,因此確??焖偾袚Q生產(chǎn)線,也是提高生產(chǎn)率的重要指標(biāo)。
低成本自動化,分為裝配LCIA和搬運(yùn)LCIA兩大項(xiàng),其中裝配LCIA比較專業(yè),這里我們說一下搬運(yùn)LCIA的基本思路。基本原則是要減少搬運(yùn)的距離、減少存取的動作、減少搬運(yùn)的距離。原材料的搬運(yùn)應(yīng)當(dāng)確保百分之百為良品、容器容量標(biāo)準(zhǔn)、多回少量巡回混載。制品的搬運(yùn)應(yīng)當(dāng)實(shí)現(xiàn)1/0一致;本工程完成的“放置點(diǎn)”,即為下個工程的“拿取點(diǎn)”;一次搬運(yùn)一個;利用低成本重力滑道;一面搬運(yùn)一面工作等。成品的搬運(yùn)應(yīng)當(dāng)做到完成的直接放入貨柜車內(nèi);采取后拉式接單生產(chǎn);生產(chǎn)交期要短于交貨交期等。
IE改善,IE工業(yè)工程學(xué)是現(xiàn)場改善的基礎(chǔ),博革咨詢將針對現(xiàn)場班組長和工程師團(tuán)隊(duì),細(xì)致講授IE實(shí)戰(zhàn)手法,帶領(lǐng)他們逐步進(jìn)行IE改善活動,確保全員參與改善活動,實(shí)現(xiàn)生產(chǎn)效率的全面提升。IE改善包含兩大內(nèi)容:制造方式的浪費(fèi)改善和管理方式的浪費(fèi)改善。其中制造方式包括工序分析、搬運(yùn)分析、運(yùn)轉(zhuǎn)分析;管理方式包括:LOB分析、作業(yè)分析、效率分析等。
PFMEA是制程失效模式及效果分析的英文簡稱。由產(chǎn)品工程師、制造工程師、質(zhì)量工程師、物流工程師、生管人員等組成的橫向?qū)<倚〗M,逐個對工位(工序)進(jìn)行現(xiàn)場審計(jì)、診斷出工位(工序)的“過程要素”是否達(dá)到“工序的目的”。
以上就是現(xiàn)場標(biāo)準(zhǔn)化的精益布局的主要內(nèi)容,完成時間約為兩周?,F(xiàn)場標(biāo)準(zhǔn)化的第二項(xiàng)內(nèi)容為“可視化”,即全面可視化現(xiàn)場。
生產(chǎn)現(xiàn)場全面可視化主要包含以下七大內(nèi)容:
第一,安全可視化——對產(chǎn)線安全設(shè)施設(shè)備進(jìn)行目視化管理,讓員工重視:危險(xiǎn)區(qū)域識別、安全天數(shù)展示、安全隱患識別,并用可視化的方式來展示具體操作步驟。
第二,質(zhì)量可視化——明確關(guān)鍵工序的位置及相關(guān)事項(xiàng),關(guān)鍵工序指標(biāo)的趨勢管理;首件產(chǎn)品封樣管理;生產(chǎn)不良品展示,識別不良品,明確不良品的判定標(biāo)準(zhǔn)和責(zé)任人員等。
第三,生產(chǎn)可視化——明確班組劃分、明確生產(chǎn)線工位名稱;明確產(chǎn)品屬性及狀態(tài);將作業(yè)指導(dǎo)書展示在現(xiàn)場;明確物流小車責(zé)任人,周轉(zhuǎn)次數(shù)等相關(guān)信息;生產(chǎn)管理文件可視化;
規(guī)定班組會議區(qū)域;時段目標(biāo)與實(shí)際產(chǎn)出可視化,及時識別異常;物料信息目視化,以免拿錯;工裝器具進(jìn)行形跡管理,易拿易管等。
第四,成本可視化——將成本的相關(guān)信息可視化,明確成本的損失點(diǎn)和控制要素。
第五,設(shè)備可視化——設(shè)備操作規(guī)程、維護(hù)規(guī)程可視化;設(shè)備名稱、設(shè)備主人、維護(hù)周期目視化;標(biāo)示計(jì)量界限范圍;明確設(shè)備的狀態(tài),正常運(yùn)行以及是否處于維修等。
第六,環(huán)境可視化——明確清掃工具放置位置,集中管理;規(guī)定水杯擺放,以免有傷產(chǎn)品;垃圾分來擺放等。
第七,人員可視化——人員培訓(xùn)后方可持證上崗;區(qū)別不同區(qū)域不同級別的人員;多技能工認(rèn)證可視化;描述班組的培訓(xùn)計(jì)劃、合理化建議、優(yōu)秀員工、5S、學(xué)習(xí)園地、員工風(fēng)采等。
以上是現(xiàn)場標(biāo)準(zhǔn)化第二項(xiàng)要素“可視化”的主要內(nèi)容,完成時間約為一周?,F(xiàn)場標(biāo)準(zhǔn)化的第三項(xiàng)內(nèi)容就是“標(biāo)準(zhǔn)化”。這里的標(biāo)準(zhǔn)化指的是管理層面的標(biāo)準(zhǔn)化,即實(shí)現(xiàn)現(xiàn)場績效的穩(wěn)定。
管理標(biāo)準(zhǔn)化遵循以下七大“標(biāo)準(zhǔn)”:
第一,數(shù)據(jù)收集標(biāo)準(zhǔn)——收集每日生產(chǎn)數(shù)據(jù),制定標(biāo)準(zhǔn)。
第二,進(jìn)度管理標(biāo)準(zhǔn)——明確現(xiàn)場管理人員的進(jìn)度標(biāo)準(zhǔn)。
第三,自工序完結(jié)標(biāo)準(zhǔn)——以關(guān)鍵工序?yàn)橹?,進(jìn)行自查互查。
第四,異常響應(yīng)機(jī)制——A3問題改善、安燈應(yīng)用、分層響應(yīng)機(jī)制、問題處理流程、異常響應(yīng)流程。
第五,現(xiàn)場早會標(biāo)準(zhǔn)——制定早會流程、會議手冊等。
第六,交接班管理標(biāo)準(zhǔn)——推廣班組長日志,明確關(guān)鍵指標(biāo)。
第七,班組績效管理——指標(biāo)討論決定、考核規(guī)定展示、績效可視化、績效核定標(biāo)準(zhǔn)可視化、月度績效考核展示、班組綜合指標(biāo)展示。
以上所有就是博革咨詢現(xiàn)場標(biāo)準(zhǔn)化的簡單介紹,如您需要更多資料或案例,請聯(lián)系客服或給我們留言。
作者:金學(xué)俊