博革行業(yè)資訊
?
豐田生產(chǎn)方式是徹底消除浪費(fèi)的方法,消除浪費(fèi)就能提高生產(chǎn)率。制造現(xiàn)場的浪費(fèi)是指「只會(huì)提高成本的要素」,存在’若不充分注意所有的地方浪費(fèi)就會(huì)逐漸增加’的性質(zhì)。因此制造產(chǎn)品的作業(yè)中, 需要有判斷怎樣的作業(yè)是浪費(fèi)作業(yè)的能力。通過豐田生產(chǎn)方式的教育來培養(yǎng)發(fā)現(xiàn)‘浪費(fèi)’的眼光。下面博革咨詢?yōu)榇蠹疫M(jìn)行精益生產(chǎn)管理七大浪費(fèi)詳解:
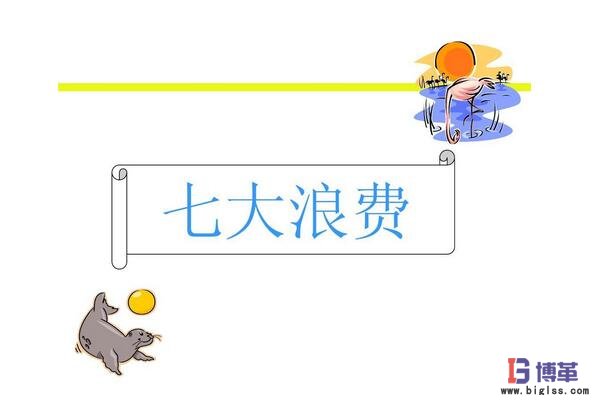
超過生產(chǎn)計(jì)劃或提前完成一點(diǎn)也不值得驕傲。這只是在浪費(fèi)的時(shí)候、生產(chǎn)了浪費(fèi)的數(shù)量的浪費(fèi)物品、制造了過盈生產(chǎn)的浪費(fèi)?,F(xiàn)如今,所有企業(yè)為了實(shí)現(xiàn)將「需要的物品,在需要的時(shí)候, 供給需要的數(shù)量」這種所謂的JIT(Just-In-Time)而展開著改善活動(dòng)。但是,對(duì)「需要的物品,在需要的時(shí)候,供給需要的數(shù)量」這句話的理解是多樣的。JIT生產(chǎn)方式所達(dá)到的狀態(tài)是指在接到顧客訂貨的同時(shí)就開始生產(chǎn),并使其在指定的時(shí)間到達(dá)到客戶手中的狀態(tài)即,發(fā)出倉庫中存在的成品庫存沒有任何意義。汽車的情況是,從確定汽車制造商的最終組裝線計(jì)劃時(shí)點(diǎn)開始生產(chǎn),但是從調(diào)配材料或部品進(jìn)行生產(chǎn),然后將產(chǎn)品運(yùn)送到各銷售點(diǎn)和代理店,并完成各種手續(xù)到達(dá)顧客手中需要最小限度的時(shí)間。
「過量生產(chǎn)的浪費(fèi)」是指進(jìn)行顧客訂貨以外的生產(chǎn)。 尤其是無視日程計(jì)劃的過盈生產(chǎn)更是荒謬。還要完全否定「 都能賣出去」的思想。為此,是以改善的觀點(diǎn)上所說的「以要求的TACT進(jìn)行生產(chǎn)」為大前提。營業(yè)和生產(chǎn)管理部門只按照交易單位的信息來生產(chǎn)是不行的
另外,制造部門若是認(rèn)為以自己會(huì)社生產(chǎn)管理部門的日程計(jì)劃進(jìn)行生產(chǎn)就一點(diǎn)問題沒有也是不行的。不要忘記信息和日程計(jì)劃都是以預(yù)測為基礎(chǔ)的,是包含「過盈生產(chǎn)」風(fēng)險(xiǎn)的。
特別是各經(jīng)銷商店是以10臺(tái)、20臺(tái)這樣的少數(shù)量來要貨。很多情況下生產(chǎn)管理部門是將這些少量訂貨以50和100的生產(chǎn)單位合并在一起下指示,發(fā)貨時(shí)從中進(jìn)行發(fā)送。于是,剩余的數(shù)量抱著「會(huì)在什么時(shí)候發(fā)出去的」的安逸心態(tài)放置,結(jié)果在幾年后的年末結(jié)算上卻成為處理損失而進(jìn)行了財(cái)務(wù)處理。
另外, 「過量生產(chǎn)」還有一個(gè)問題點(diǎn)。企業(yè)不管采用什么方法,所確立的都是以月為單位進(jìn)行生產(chǎn)的體制。雖然是以生產(chǎn)計(jì)劃為基礎(chǔ)來研究制定加班計(jì)劃、設(shè)備運(yùn)轉(zhuǎn)計(jì)劃、材料部品的調(diào)撥計(jì)劃等,但每個(gè)方面自不能有多余部分以免形成投入的余量。于是在實(shí)際生產(chǎn)中,若過多制造某特定部品,就不能制造其他的部品。現(xiàn)在重要的不是要實(shí)現(xiàn)合計(jì)數(shù)量而是要嚴(yán)守各部品別的計(jì)劃。通常, 都是不責(zé)怪多生產(chǎn)部品的行為而是只追究少生產(chǎn)部品的行為, 這樣的管理不能稱為管理。
2、庫存的浪費(fèi)
多余的部分作為過盈生產(chǎn)所產(chǎn)生的浪費(fèi),在豐田生產(chǎn)方式中將其稱為最不好的浪費(fèi)。這部分是因機(jī)器的增設(shè)、材料的事前入庫、多余的作業(yè)者、利息的增加、倉庫的增大等而導(dǎo)致的,是有百害而無一利的部分。庫存與產(chǎn)品產(chǎn)生附加價(jià)值沒有任何關(guān)系。庫存只會(huì)掩藏生產(chǎn)和流通中所發(fā)生的問題點(diǎn),因此,要減少庫存,越少越好。
因庫存而產(chǎn)生的問題點(diǎn)數(shù)也數(shù)不完。因庫存而產(chǎn)生確保保管庫存的倉庫和容器、出入庫的搬運(yùn)器具和人員、管理庫存的各種機(jī)器帳表以及人員的有關(guān)費(fèi)用,以及在成為長期積壓庫存情況下的質(zhì)量保證費(fèi)用和處理損失費(fèi)用等。一般需要15 ~ 20%左右產(chǎn)品單價(jià)的維持費(fèi)。特別是高價(jià)產(chǎn)品和體積大的產(chǎn)品會(huì)達(dá)到30 ~ 35%。另外,因存在庫存,眾多的問題點(diǎn)不能顯露出來(可視化),而且企業(yè)的生產(chǎn)體質(zhì)絕對(duì)強(qiáng)化不起來。因此,將庫存當(dāng)做「罪過」而努力削減。庫存只是管理·監(jiān)督者為了高枕無憂而準(zhǔn)備的安心劑。
3、搬運(yùn)的浪費(fèi)
JIT 生產(chǎn)是從搬運(yùn)開始的這種說法一點(diǎn)也不過分。要認(rèn)識(shí)到從手「伸出」「移動(dòng)」「拿來」「放下」開始, 臺(tái)車(Pallet)的移動(dòng),「由倉庫到工廠」「由工廠到機(jī)器」在「作業(yè)者的手所涉及的范圍」移動(dòng)等,這些全部都是不合理。只是單純地從工廠內(nèi)的一個(gè)地方移動(dòng)到另一個(gè)地方這種物流,其間絕對(duì)不會(huì)產(chǎn)生附加價(jià)值。不是要改善搬運(yùn)作業(yè)的行為本身,而是要消除它,消除得越多,競爭力就越會(huì)增加。
最小限度的搬運(yùn)是指「ONE WORK·ONE TOUCH」。搬運(yùn)雖然是生產(chǎn)中必不可少的作業(yè),但要將其減到最小限度是關(guān)鍵(POINT)。改善「搬運(yùn)」可以考慮進(jìn)行自動(dòng)化和使用無人搬運(yùn)車,但首先要考慮廢棄搬運(yùn)本身。從工程的布局來看,可以說「全程連續(xù)的LINE化」是理想布局。若只將一部分工程設(shè)置在工程之外, 或雖是同一工程卻將要進(jìn)行全程連續(xù)作業(yè)的工程設(shè)置在不同的建筑物內(nèi)就會(huì)發(fā)生浪費(fèi)的搬運(yùn)。由于存在不這樣做就不行的理由和企業(yè)的方針,因而不能一律地判斷是好是壞,但,這是浪費(fèi)一點(diǎn)錯(cuò)沒有。為了進(jìn)行全程連續(xù)流水線化, 需要解決技術(shù)和工藝方法的開發(fā)、設(shè)備可靠性和靈活性的改善, 以及采購政策的研究等多項(xiàng)課題。而且,對(duì)LINE內(nèi)各工程間的間隔,為了「修理」要達(dá)到能拽出產(chǎn)品的最小限度。雖然根據(jù)設(shè)備的大小要有所不同, 但設(shè)備長度在2 ~ 3m的情況工程間最大間隔限在10 ~ 20cm 左右就可以。為此,需要將設(shè)備的各種閥門、開關(guān)、儀表、機(jī)油容器等從側(cè)面移到前面或后面, 設(shè)備設(shè)計(jì)面上的研究是最關(guān)鍵的要點(diǎn)。并且工程內(nèi)放置部品的場所?諞宰勻壞淖聳粕焓志湍蘢プ〔返姆段?而不需要向前彎身或踮腳,或轉(zhuǎn)身,即,正常是在60 ~ 70cm 以內(nèi)。以購入品的包裝單位大為理由而臨時(shí)放在線體的旁邊少量地分批拿出來使用,由于這也是移動(dòng),因而需要改善。
4、等待的浪費(fèi)
機(jī)器自動(dòng)加工時(shí)只是在旁邊站著監(jiān)視的作業(yè)方法即使作業(yè)者想要做什么,可由于機(jī)器在運(yùn)轉(zhuǎn)而沒辦法作業(yè)從而產(chǎn)生了浪費(fèi)。是因等待作業(yè)的富余時(shí)間而產(chǎn)生的浪費(fèi)。但是由于這種浪費(fèi)易于發(fā)現(xiàn)而且不會(huì)誘發(fā)別的浪費(fèi),所以比別的浪費(fèi)容易改善。由于現(xiàn)場管理者是考慮了單位的環(huán)境和作業(yè)因素來直接創(chuàng)建現(xiàn)場的人,因而對(duì)現(xiàn)場有自豪感,所以看不出等待的浪費(fèi)。而且根據(jù)自己的想法發(fā)表著「這個(gè)作業(yè)就是這樣。多少會(huì)有些等待, 但由于做了最大限度的改善,而難以進(jìn)一步改善」這樣的見解。 這些人中有很多人認(rèn)為「由于人不是機(jī)器人, 所以不能1秒、2秒一點(diǎn)不差地滿負(fù)荷作業(yè)。是需要有少量余量的」。是存在象組裝作業(yè)一樣沒有等待作業(yè)的地方的。在「同樣的勞動(dòng), 同樣的報(bào)酬」的觀點(diǎn)上,消除等待也可以說是現(xiàn)場管理者的重要任務(wù).
5、動(dòng)作的浪費(fèi)
指的是在產(chǎn)品的制造過程中沒有附加價(jià)值的人的行動(dòng)或設(shè)備、機(jī)器的動(dòng)作。找部品或制造不良品等…。作業(yè)場所中能發(fā)生浪費(fèi)的原因要多少有多少而且無時(shí)不在。工廠里的所有事物都在動(dòng),人們步行、說話、打電話、開會(huì),機(jī)器也在運(yùn)轉(zhuǎn), 水也通過管道流動(dòng),全部都是動(dòng)態(tài)的活動(dòng)。但是不是所有的動(dòng)作都給產(chǎn)品帶來附加價(jià)值,不能給產(chǎn)品帶來附加價(jià)值的活動(dòng)就是浪費(fèi)。動(dòng)作的浪費(fèi)是十分細(xì)小行動(dòng)的浪費(fèi)。因此動(dòng)作的浪費(fèi)具有很不易被發(fā)現(xiàn)的性格。例如, 為了拿住部品而進(jìn)行方向轉(zhuǎn)換, 固定夾具時(shí)多次調(diào)整的動(dòng)作,或者是安裝時(shí)按壓的動(dòng)作等等,有很多象這樣非常細(xì)微的動(dòng)作。將持續(xù)按壓部品和開關(guān)的動(dòng)作稱做按摩,按摩不要在公司做,還是回家給老婆做比較好,
工廠沒有理由在按摩上花錢。動(dòng)作的浪費(fèi)由于極其細(xì)小,所以要仔細(xì)觀察 「一舉手一投足」,并通過動(dòng)作分析進(jìn)行改善。要修整夾具和產(chǎn)品的形狀、精密度, 以徹底遵守標(biāo)準(zhǔn)作業(yè)。
6、加工的浪費(fèi)
產(chǎn)品是要對(duì)原材料進(jìn)行某種形態(tài)的加工才能做出來,有多種加工的方法,這若干種方法中的哪種方法能比別的方法更有效, 而哪種方法又不如別的方法呢,要進(jìn)行不斷的改善。“從很早以前到現(xiàn)在一直都是這樣做的,而且別人也都在這樣做”等這樣的思考方式是不能提高競爭力的?!讣庸さ睦速M(fèi)」是最能顯示技術(shù)力的地方。在電弧焊中,您想使機(jī)器手產(chǎn)生火花的百分比達(dá)到多少呢?若是60%, 那么,若不具備部品固定方法以及與他工程的編成方法、部品的設(shè)置方法和線路管理或部品的精密度等多種條件,也是達(dá)不到該數(shù)值的。而且,即使是產(chǎn)生火花和切削碎屑的作業(yè), 有過多消除毛刺和磨邊作業(yè)的加工也是問題。這不是以自己會(huì)社的水準(zhǔn)來判斷的,而是要掌握競爭會(huì)社的信息和加工業(yè)種的水平,以與高水平進(jìn)行比較來判斷的。 若只是以自己會(huì)社的水準(zhǔn)來判斷而在競爭中敗下陣來,那就什么也不是了。
7、不良的浪費(fèi)
不良的發(fā)生確實(shí)是擋不住程度的巨大浪費(fèi)。制造不良品由于是制造了賣不出去的產(chǎn)品, 也就是制造了浪費(fèi)的產(chǎn)品。雖說如今已經(jīng)沒有必要再對(duì)「不良」其本身進(jìn)行討論, 可現(xiàn)實(shí)又如何呢?向消費(fèi)者提供良品是進(jìn)行企業(yè)活動(dòng)的大前提。為了這些消費(fèi)者,不是要依靠最終工程的檢查或挑選來保證的, 而是要在各工程內(nèi)達(dá)到絕對(duì)不產(chǎn)生不良品來進(jìn)行制造的??墒? 雖然制定了這樣的方針, 但現(xiàn)實(shí)上卻不能說是徹底達(dá)到了。在「徹底保證自己工程的品質(zhì)」的帷幕下有很多裝有不良品的不良品箱。倘若這些不良品箱以1個(gè)月或1周的量堆放,則證明改善沒有得到實(shí)行。特別是,有時(shí)會(huì)發(fā)現(xiàn)在鑄造、壓鑄、樹脂等中存在 「若能熔化就再使用」或在機(jī)器加工中存在「尺寸再大一點(diǎn)還行」等RECYCLE(循環(huán)利用)的想法。這是荒謬的錯(cuò)誤。說出這中話的現(xiàn)場管理者是沒有資格的。以某企業(yè)為例,若產(chǎn)生了一個(gè)不良, 部品的價(jià)格上就產(chǎn)生3倍的費(fèi)用。不良不僅在費(fèi)用層面上負(fù)擔(dān)相當(dāng)大,更重要的是反映了企業(yè)在對(duì)待顧客的姿態(tài)上有問題。若要消除不良的浪費(fèi),關(guān)鍵是通過遵守規(guī)定的技術(shù)加工條件,進(jìn)行徹底的標(biāo)準(zhǔn)作業(yè)來保證質(zhì)量,而且,重要的是還要針對(duì)細(xì)小的問題,向設(shè)備·夾具和產(chǎn)品設(shè)計(jì)的流程流逆流而上來推進(jìn)改善活動(dòng)。
博革業(yè)務(wù)
歡迎您訪問博革咨詢官網(wǎng)!博革咨詢是中國首家整合精益生產(chǎn)/六西格瑪/流程再造的咨詢公司,專注于提供精益生產(chǎn)、6S現(xiàn)場管理、TPM設(shè)備管理、精益工廠布局、專業(yè)目視化、精益供應(yīng)鏈、精益研發(fā)、六西格瑪管理、智能制造等綜合性問題解決方案并負(fù)責(zé)落地實(shí)施。
全國咨詢熱線:021-62373515、157-2153-3189
【精美PPT】MSA測量分析系統(tǒng)培訓(xùn)課件完整版170頁
【簡介】 本PPT 為博革咨詢精選課件-MSA測量系統(tǒng)實(shí)戰(zhàn)培訓(xùn)教材,主要講述 測量系統(tǒng)的基本概念,測量系統(tǒng)分析計(jì)劃,連續(xù)和離散數(shù)據(jù)測量系統(tǒng)分析以及參考數(shù)據(jù)和Minitab操作案例...... 注 /about/news/down/1943.html
【精美PPT】MSA測量系統(tǒng)分析實(shí)戰(zhàn)培訓(xùn)教材PPT-99頁
【簡介】 本PPT 為博革咨詢精選課件-MSA測量系統(tǒng)實(shí)戰(zhàn)培訓(xùn)教材,主要講述 測量系統(tǒng)的基本概念,測量系統(tǒng)分析計(jì)劃,連續(xù)和離散數(shù)據(jù)測量系統(tǒng)分析以及參考數(shù)據(jù)和Minitab操作案例...... 注 /about/news/down/1942.html
【精美PPT】QFD質(zhì)量功能展開培訓(xùn)精編課件PPT-48頁
【簡介】 本PPT 為博革咨詢精選課件,主要講述QFD質(zhì)量功能展開的概述、起源和用處,QFD展開假設(shè)的條件、QFD展開流程 、以及QFD展開的具體步驟...... 注意: 完整PPT共 48 頁,附件下載內(nèi) /about/news/down/1924.html