什么是標準作業(yè)?
日期:2017-11-07 / 人氣: / 來源:m.wtport.com / 熱門標簽:
歡迎您訪問博革咨詢官網(wǎng)!博革咨詢是中國首家整合精益生產(chǎn)/六西格瑪/流程再造的咨詢公司,專注于提供 精益生產(chǎn)、6S現(xiàn)場管理、TPM設備管理、精益工廠布局、專業(yè)目視化、精益供應鏈、精益研發(fā)、六西格瑪管理等綜合性問題解決方案并負責落地實施。
全國咨詢熱線:021-62373515、157-2153-3189
我們承諾:見效快、易復制,目標必對賭!
豐田生產(chǎn)方式聞名于世界,它不是對泰勒科學管理方式的照搬,而是加以改善創(chuàng)新,逐步形成自身獨特的一套管理模式,豐田標準化作業(yè)才用了網(wǎng)絡化、有彈力與創(chuàng)新的制度。
現(xiàn)代的社會環(huán)境與市場環(huán)境是,客戶需求的變化越來越快,一線員工流動率越來越高,人工成本不斷升高,動態(tài)用工和結構性用工成為必然。因此,現(xiàn)代企業(yè)必須保持高質(zhì)量、高效率、低成本和快速應變的競爭優(yōu)勢,才能在競爭中生存下來。標準化管理是應對市場新情況的最有效力式。
所謂標準化是指,為了實現(xiàn)整個工作過程的協(xié)調(diào)運行、提高工作效率,而對作業(yè)的質(zhì)量、數(shù)量、時間、程序、方法等制定統(tǒng)一規(guī)定,做出統(tǒng)一標準,也就是對人所從事的工作標準化。
作業(yè)標準化、標準化作業(yè)、變化點管理和改善優(yōu)化是標準化作業(yè)管理的動態(tài)循環(huán)。日本和美國的企業(yè)實踐證明:作業(yè)標準化做得越好,對員工技能的依賴越低,新員工上手就越快;標準化作業(yè)做得越好,生產(chǎn)人員越有條件進行變化點管理,一線干部越有時間推進改善優(yōu)化;不斷改善和優(yōu)化的結果,是使企業(yè)作業(yè)標準化體系不斷完善并得到動態(tài)維護。所以,“鐵打的營盤流水的兵”,日本和美國在華企業(yè)甚至能用高達40%以上的季節(jié)性用工,還能保持強勢的市場競爭力,標準化作業(yè)管理功不可沒。
其實,標準化作業(yè)管理由來己久,并且在19世紀中后期至20世紀初得到迅速發(fā)展。這一時期,資本主義經(jīng)濟迅猛發(fā)展,然而,管理水平還很低下,仍處于經(jīng)驗管理階段,工人勞動效率低、浪費嚴重,尋找一種合理有效的生產(chǎn)管理方式,成為亟待解決的課題。
大野耐一認為“標準化工作程序說明表及其中包含的信息是豐田生產(chǎn)方式中的重要組成部分。一位生產(chǎn)線工作者要寫出一份讓其他人能夠明白的標準化工作程序說明表,他必須相信這份說明表的必要性……避免瑕疵產(chǎn)品、操作失誤、意外狀況等重復發(fā)生,并納入工作者的想法,這樣才能維持高生產(chǎn)效率”。在這種情況下,誕生了泰勒的科學管理理論。
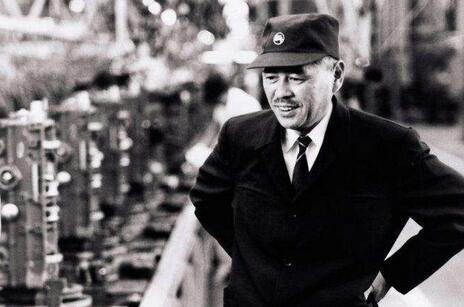
于是,在那一時期西方國家的工廠里,無論是制定勞動定額、工時定額、作業(yè)計劃還是成本核算,最后都要形成標準。因此,工作標準化在極短的時間成長、發(fā)展起來。
第二次世界大戰(zhàn)以后,日本積極引進泰勒制,通過制定包括工作標準在內(nèi)的一系列標準,使企業(yè)管理取得顯著的效果。為日本工業(yè)的迅速復蘇做出了卓著貢獻。
可是,豐田沒有照搬泰勒的科學管理方法,而是在此基礎之上,創(chuàng)造性地形成了自己的管理模式。豐田認為,企業(yè)要想在所屬的行業(yè)內(nèi)保持領先的地位,要有強于對手的競爭力,就必須制定出確實可行的、能授權員工的標準,只有這樣,才能持續(xù)改進重復性流程。而要充分授權員工,就必須首先把員工當作問題的解決者,而不是只知道接受命令的工具。
這樣一來,豐田把傳統(tǒng)企業(yè)管理中,官僚式由上而下的企業(yè)制度取消了,而采取了網(wǎng)絡化、有彈性與創(chuàng)新的制度,這就是豐田的標準化作業(yè)。
在豐田公司,標準化并不是泰勒時代的“明確寫出操作員必須遵循的工作步驟”。具體來說,豐田公司標準化作業(yè)具有以下3個特點:
1.由現(xiàn)場監(jiān)督人員決定具體的標準作業(yè)
在以往公司,標準作業(yè)一般由IE人員來決定。而在豐田汽車公司,標準作業(yè)的各項組成要素,主要是由現(xiàn)場監(jiān)督人員具體決定的。比如:組長、班長有權決定各臺設備生產(chǎn)一個單位產(chǎn)品需要的作業(yè)時間和各個作業(yè)人員應該完成的各種作業(yè)的順序。在制定標準作業(yè)后,組長和班長必須親自對這個標準完全掌握、了解,并且現(xiàn)場操作,以使作業(yè)人員可以對此標準作業(yè)完全理解、服從。
豐田認為,只有對現(xiàn)場作業(yè)及操作人員非常了解的人才適合作為標準作業(yè)的制定者,而班長、組長最符合這個要求。也只有這種標準作業(yè)才具有可行性、公平性,也激發(fā)了員工的主人翁意識。
2.標準化作業(yè)分為五個特定程序
(l) 確定循環(huán)時間。
?。?) 確定一個單位產(chǎn)品的完成時間。
?。?) 確定標準作業(yè)順序。
(4) 確定在制品的標準持有量。
?。?) 編制標準作業(yè)書。
3.用循環(huán)時間對作業(yè)人員進行再分配
對作業(yè)人員進行再分配指的是,按生產(chǎn)一個單位產(chǎn)品所必需的不同作業(yè)數(shù)目和作業(yè)人員人數(shù),對人員和材料進行重新分配,以減少作業(yè)流程中人員使用量。
由此看來,豐田公司的標準化并不是那種強加于員工的工作標準化,而是把標準化當作一種授權,以提高工作效率、激勵員工不斷創(chuàng)新。豐田標準化為企業(yè)創(chuàng)立了共同合作的團隊,解決了勞資關系,因而把以前被視為不利或無效的標準化,變成了有利、有效益的項目。
豐田認為,要實現(xiàn)持續(xù)改進,必須先把流程標準化。如果,作業(yè)流程雜亂無章法,經(jīng)常改變,任何針對此流程所做的改進都是無用的。因此,豐田公司的標準化不僅僅是使作業(yè)人員的工作可重復且有效率。豐田的標準化己經(jīng)應用到白領階層的工作流程中,在豐田公司任何一個角落我們都可以看到標準化的影子。
當豐田公司要開發(fā)新的產(chǎn)品,組織新的生產(chǎn)線時,是怎樣制定新的標準化的呢?比如,一個企業(yè)在一個陌生領域,要投入資金,新產(chǎn)品開發(fā)時,怎么把不可避免的混亂情形標準化呢?豐田公司的做法是以均衡的方式把工作標準化。當一項新產(chǎn)品處于早期計劃階段時,他們先把代表工廠所有部門領域的人員全部聚集在一個開放式辦公室,形成一支大團隊,稱為“先導團隊”。“先導團隊”不僅協(xié)助生產(chǎn),還和工程部門攜手合作,發(fā)展最初的標準化工作,以在此產(chǎn)品剛推出時使用這些標準化工作,然后再把它交給生產(chǎn)團隊,尋求進一步改進。
在豐田公司,標準化作業(yè)的目的,是通過必要的、最小數(shù)量的作業(yè)人員進行有效生產(chǎn)。豐田公司的標準化,首先保證了產(chǎn)品的高質(zhì)量。在豐田公司,當制件被發(fā)現(xiàn)有瑕疵時,作業(yè)人員被問的第一句話是:“有沒有按照標準化工作執(zhí)行?”接著,在解決問題時,監(jiān)督管理者會看著操作人員按照標準化工作說明表中規(guī)定的步驟重新執(zhí)行一遍。如果發(fā)現(xiàn)不是操作人員的問題,他的操作完全遵循了標準化作業(yè)表,那就表示這些標準步驟必須加以修正:如果發(fā)現(xiàn),是由于操作人員的執(zhí)行錯誤,而導致瑕疵產(chǎn)品,此作業(yè)人員便會受到相應的懲罰。
實際上,豐田后一種情況發(fā)生的概率非常小。去過豐田公司的人都知道,那里的標準作業(yè)程序說明表并不是張貼在工作場所內(nèi)。所有的作業(yè)人員都受過執(zhí)行標準化工作的訓練,每個人都必須做到不看表一樣能準確無誤地執(zhí)行標準化作業(yè)。
其次,標準化作業(yè)提高了生產(chǎn)率。因為,標準化讓許多無效勞動不再出現(xiàn)在生產(chǎn)作業(yè)中,既提高了工作效率,又激發(fā)了員工的工作積極性。標準化使均衡化生產(chǎn)成為可能,因為,在實現(xiàn)標準化的過程中,“循環(huán)時間”或者說均衡化理念就己經(jīng)很好地貫徹到作業(yè)中了。標準化作業(yè)也有助于減少庫存浪費。標準化作業(yè)中,制品的“標準持有量”在消除多余的在制品庫存力面有潛在的力量。
作者:博革咨詢